Optimierte Fertigung von Leichtbau-Dachsystemen Dank KI
Als innovativer Systemlieferant beliefert Webasto nahezu alle großen Automobilhersteller. Das Kerngeschäft des Weltmarktführers für Dachsysteme umfasst die Entwicklung und Produktion von Panorama-, Schiebe- sowie Cabriodächern und Standheizungen. Mit Batteriesystemen und Ladelösungen bietet der Zulieferer auch Produkte für die Elektromobilität an.
Im Geschäftsjahr 2019 produzierte Webasto mehr als 11,9 Millionen Dachsysteme. In vielen davon kommt Polycarbonat, ein besonders leichter Kunststoff, zum Einsatz. Dieser eignet sich hervorragend für den Fahrzeugbau, da er eine Vielzahl an Vorteilen vereint. So sind Komponenten aus Polycarbonat fast 50 Prozent leichter als baugleiche Teile aus Glas, ebenso transparent und dabei extrem schlagzäh. Ein weiterer Vorteil bei Bauteilen aus Polycarbonat, die Webasto im Zwei-Komponenten-Spritzgießverfahren herstellt, ergibt sich aus der hohen Formbarkeit und der damit verbundenen Designfreiheit.
Polycarbonat – ein Kunststoff mit hohen Ansprüchen
Die Vorteile liegen also klar auf der Hand. Aber es gibt auch Herausforderungen! Denn die Herstellung der Dachelemente aus Polycarbonat ist äußerst anspruchsvoll. Um diesen Anforderungen gerecht werden zu können, werden große Spritzgussmaschinen benötigt, die das komplexe Spritzgießverfahren beherrschen. Hinzu kommen aufwendige Spritzgusswerkzeuge für die unterschiedlichen Verfahren wie Parallelprägen und Expansionsprägen, die dafür mit der entsprechenden Sensorik und dem entsprechenden Heißkanal ausgestattet sind. Zur Erreichung der hohen Qualitätsansprüche ist zudem eine punktgenaue Einhaltung der sehr engen Toleranzen im Fertigungsprozess unerlässlich.
Am Anfang war das MES
Damit sich die Investition in eine solche Anlage langfristig rechnet, müssen Stillstandzeiten, Ausschuss und andere Störgrößen auf ein absolutes Minimum reduziert werden. Um das zu erreichen, arbeitet Webasto unter anderem mit einem Manufacturing Execution System (MES), das die einzelnen Bauteile über ihre Seriennummer automatisch registriert, die jeweiligen Qualitätsdaten erfasst und mögliche Abweichungen sowie Fehler zeitnah meldet.
Webasto entschied sich für eine Erweiterung des bestehenden MES in seinem Kunststoff-Kompetenzzentrum im bayerischen Schierling. Die im MES vorliegenden Daten sind jedoch nur bedingt dafür geeignet, um zeitnah und unverzüglich auf Prozessveränderungen reagieren zu können.
Die Ursachenanalyse der MES-Daten ist meist sehr aufwendig und zeitintensiv. Daher suchte Webasto nach einer Ergänzung zum bereits bestehenden System, um Störungen im Prozess effizienter, schneller und damit auch kostengünstiger zu eruieren. Diese sollte neben den bauteilbezogenen Daten vor allem auch spritzgussbezogene Prozessinformationen aus den Maschinen, den Heißkanalreglern, der Werkzeug-Temperierung und der Sensorik erfassen und alle Daten letztendlich miteinander in Verbindung bringen.
Zm Einsatz kommt dabei das skalierbare KI-System ‚Detact‘ von Symate. Detact erweitert das MES in den für Webasto wichtigen Bereichen.
Technologiedatenmanagement on Top
Kurz nach der Entscheidung für den Einsatz von Detact wurde die Software für ein erstes Pilotprojekt an einer Spritzgussmaschine in Schierling eingerichtet. Das browserbasierte System war innerhalb kurzer Zeit installiert und wenig später startete die Analyse der zum Teil hoch komplexen und heterogenen Daten.
„Detact zieht sich die Bauteildaten, wie den DMC und die Qualitätsdaten einfach aus MES und erfasst zusätzlich noch Maschinen- und Peripheriedaten“, freut sich Dawid Danielak, ein erfahrener Anwendungstechniker bei Webasto, der die Einführung von Detact von Anfang an mit begleitet.
„Alle relevanten Parameter wie der Maschinenstatus und vordefinierte Soll- bzw. Grenzwerte sind in Detact verfügbar und werden über spezielle Apps nutzbar. Daher arbeiten wir jetzt z.B. mit der ‘Process Exploration-App‘, der ‚Exploratory Data Analysis-App‘ und der ‚Anomaly Detection-App‘. Schon nach kurzer Zeit konnte das selbstlernende System mit allen wichtigen Daten umgehen und war dazu in der Lage, mögliche Fehlerquellen zu erkennen und diese aufzuzeigen. Als ein Update für unser bestehendes MES bevorstand und wenig später noch das Forminnendrucksystem aktualisiert werden musste, waren wir etwas skeptisch. Doch in beiden Fällen erwiesen sich die Bauchschmerzen als unbegründet, denn das Team von Symate hat die Anpassungen innerhalb weniger Stunden integriert und alle Änderungen berücksichtigt.“
Bereits während der Testphase wurde eine Monitoring-Funktion eingerichtet, die die Pilotanlage mit ihren jeweils aktuellen Betriebszuständen und Parameterwerten (z.B. Zykluszeit) live visualisiert. Hier kann Webasto bspw. die Mittelwerte der Zykluszeiten für einen Tag ablesen und Toleranzverletzungen erkennen. Ebenfalls integriert sind Parameter für relative Ausschusszahlen sowie eine Bauteilhistorie inklusive der Recherche nach Bauteilen und der Darstellung aller hinterlegten Fertigungsparameter bzw. Messwerte. Durch die in Detact integrierte, schussbezogene Synchronisierung der Daten wird hier eine automatisierte Zuordnung der hinterlegten Daten zu den Bauteilen realisiert, obwohl dies in den Ursprungsdaten nicht vorhanden ist. Dadurch wird z.B. die Analyse und Recherche nach Bauteilen bei Qualitätsrückläufern möglich.“
„Nachdem das Pilotprojekt unsere Erwartungen erfüllt hat, haben wir uns daher in 2019 entschieden, alle weiteren Anlagen der Spritzerei in Detact abzubilden“, ergänzt Matthias Altendorfner. „Außerdem haben wir uns entschieden, zusätzliche Detact-Apps wie Downtime Analysis, Component History, Process Performance und Smart Data Cockpit zu integrieren. Der Ausbau ist derzeit noch im Gange, aber er läuft bis dato reibungslos. Unsere Vision ist, dass Detact nach Abschluss dieser Phase quasi vollautomatisch arbeitet. So soll das System beispielsweise ganz einfach eine E-Mail schicken, wenn Toleranzen verletzt oder Anomalien erkannt werden – und das mit den Informationen, die wir im entsprechenden Fall wirklich brauchen.“
Alles in allem – Prozesstransparenz und klare Fakten
Mit der Einführung von Detact wurde die Polycarbonat-Spritzgießfertigung bei Webasto spürbar optimiert – schnellere und effizientere Prozessanalysen führen zu einer merklichen Reduzierung des Ausschusses. Zudem haben die Mitarbeiter einen umfassenderen Zugriff auf alle Parameter, die für die Fertigung eines Bauteils relevant sind. Und: Sie verstehen die Korrelation der einzelnen Prozessparameter auf die Qualität nun deutlich besser. Auf dieser Basis können sie jederzeit schnell Entscheidungen treffen und den jeweils aktuellen Prozess punktgenau anpassen.
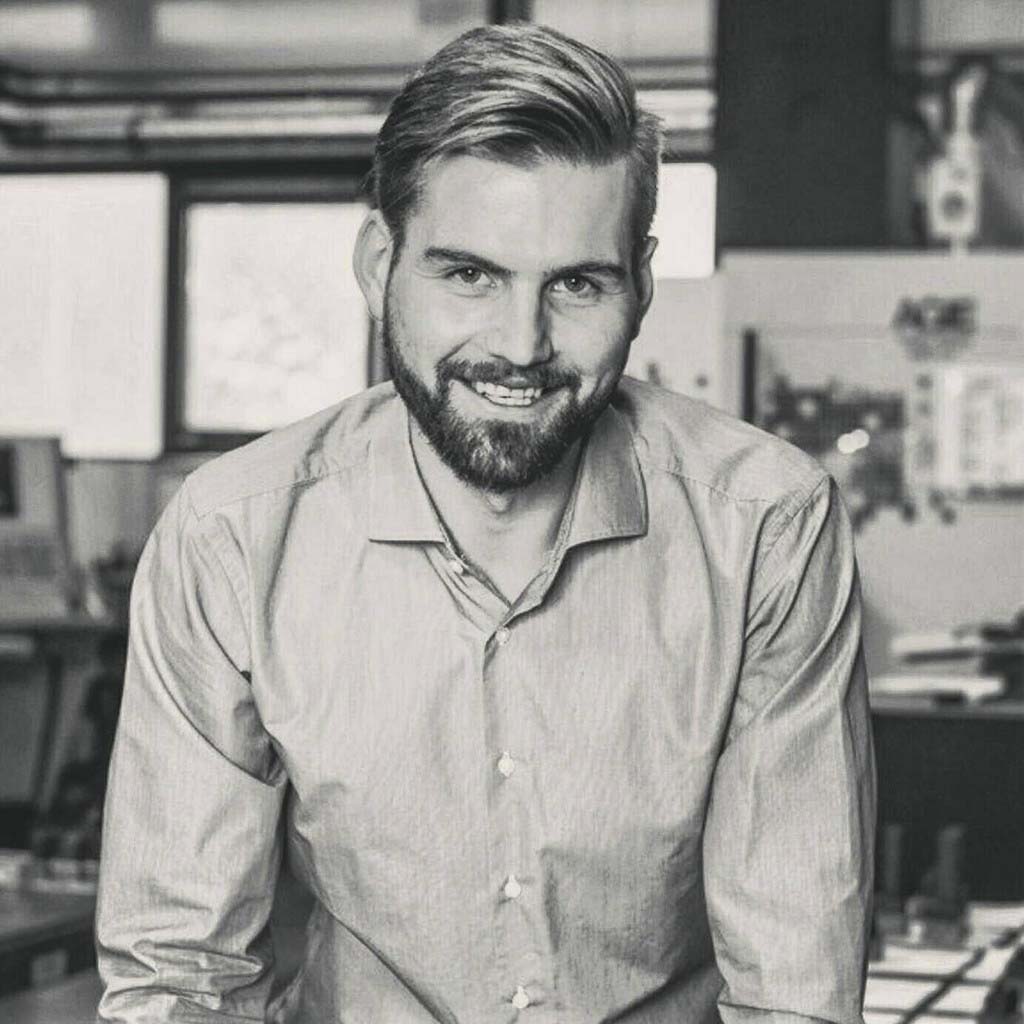
David haferkorn
Das könnte Sie auch interessieren:
So nutzen unsere Kunden Detact!